Technology is seen as a tool or enabler to help people to improve the quality of life (QoL). With rapid advancement in technology, components are getting smaller and better to serve people and the world. Research is fast becoming an essential skill to lead the way.
The Nagaoka Review had an interesting interview with Nam, a first year doctoral program student at the Nagaoka University of Technology to share more about his research and thoughts for the future.
NR: The Nagaoka Review ; Nam: Ha Phuong Nam
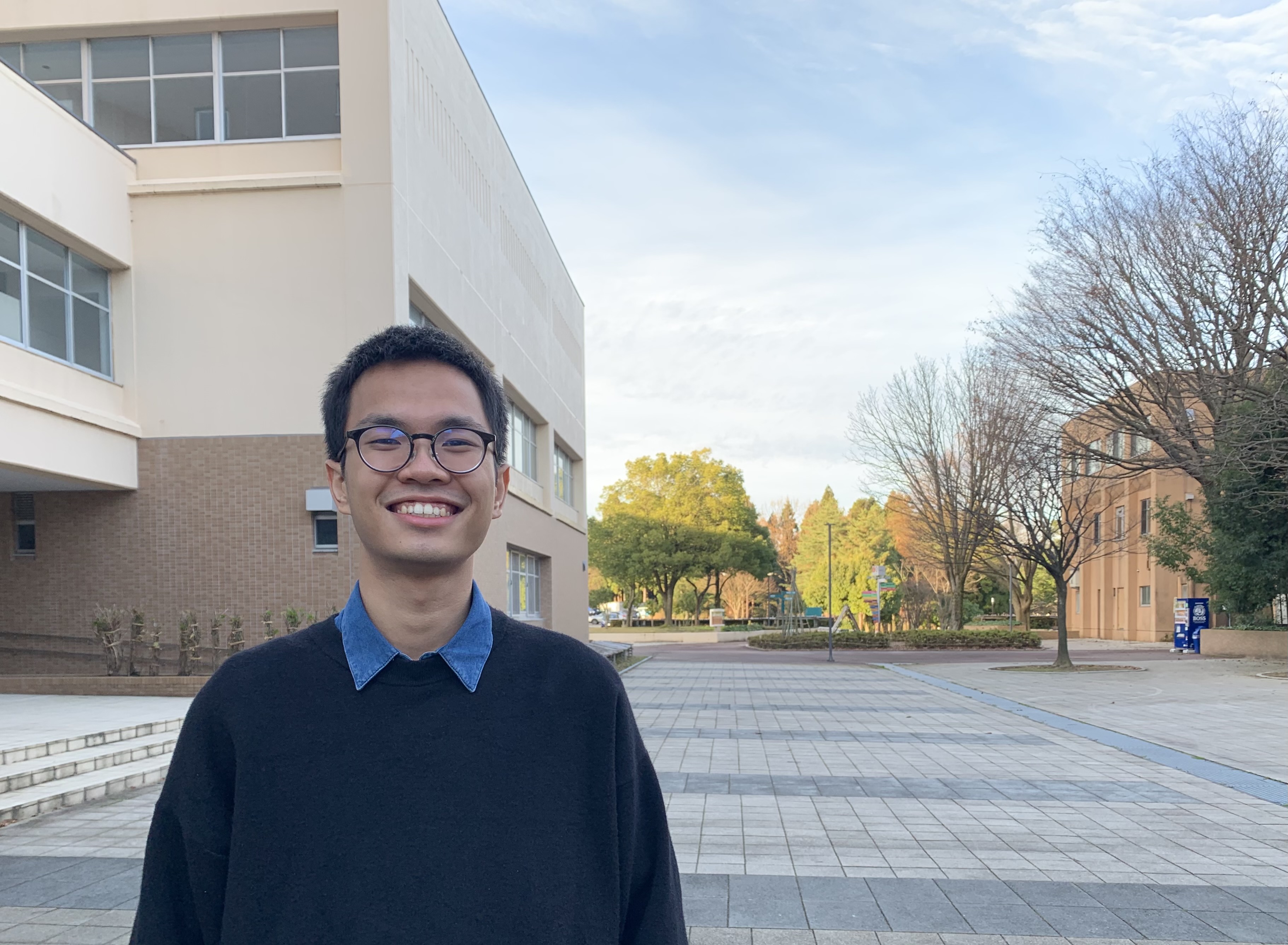
Nam at the Nagaoka University of Technology campus at Nagaoka, Niigata Prefecture
NR: Thank you for taking time to speak with us! Could you share a little about yourself?
Nam: My name is Ha Phuong Nam, but please call me Nam. I’m from Hanoi and this is my third year at Nagaoka. I am currently a first year Ph.D student at the Micronano Processing Lab, or fondly known as the “Mizoshiri Lab” by our lab mates.
I research on microfabrication to fabricate micro 3D structure of metal that is about 10 microns. To put things into perspective, the width of one strand of hair is about 100 microns. I am working on micro 3D structure that is 10 times smaller than hair. Almost every device we have contain micro components. But due to its size, people tend not to notice it and take it for granted.
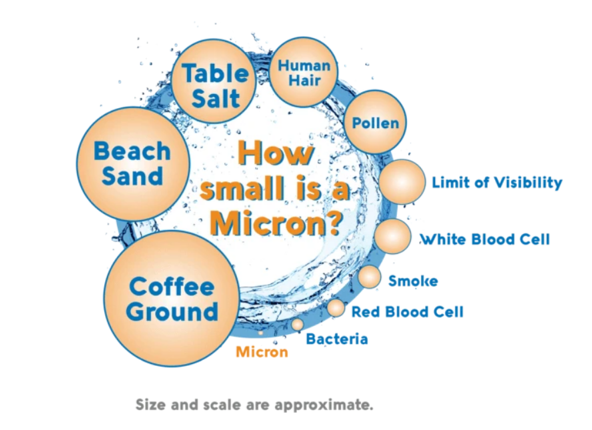
Illustration of the size of a micron. Image via Freshwater Systems
NR: Could you tell us more specifically about what you are working on?
Nam: I am currently working on using femtosecond laser irradiation of special material in order to fabricate micro 3D metal pattern metal such as copper which is used as wires.
The challenge of conventional methods is using step by step process and vacuum environment which is costly and not environmentally friendly. In my research, I use femtosecond laser to irradiate a thin film of special material containing metal ion. With the material being transparent, the laser beam could penetrate the thin film and the laser irradiation can cut the connections between the metal ion and another locally. To put it in a simple way, it means only a part of the connection irradiated by the laser will be cut. The action of cutting the connection allows pure metal to be generated from the inside of the original material thin film. As for the non-irradiated part, it could be easily removed using water. I apologize for such scientific discussion, but I hope it is easy to understand!
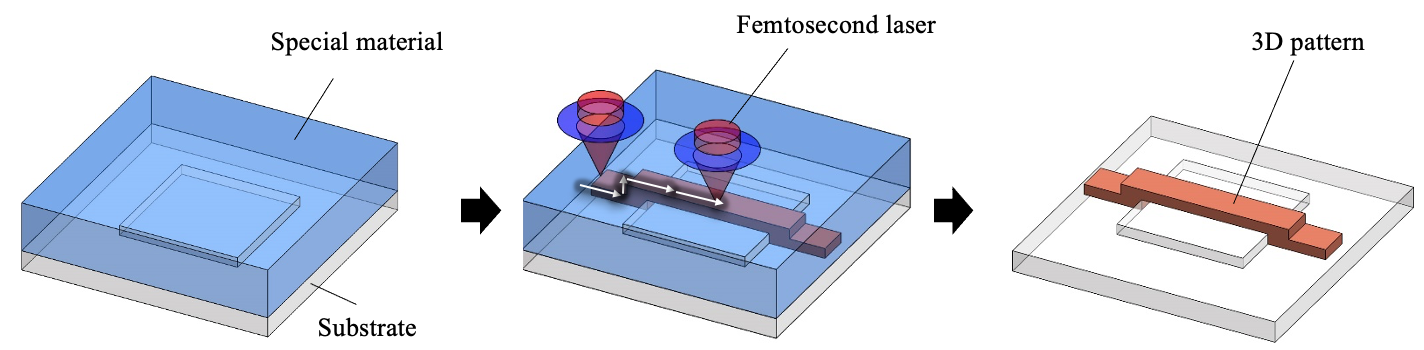
An illustration of Nam’s research. Image courtesy of Nam.
NR: It sounds challenging but thank you for making it easier to understand! What is the insight you have gained from this?
Nam: The interesting insight gained is that metal can be generated inside the thin film through this process. When working with metal, oxidation is a problem especially during the generation of pure metal. Time is needed for metal to be stable before becoming pure metal after the connections are cut (without being oxidized). When there is air, the reaction between unstable metal and oxygen would result in oxidation. So, the biggest takeaway from my research is this: Due to metal being generated inside the thin film, it means there will be no air around to cause oxidation.
NR: After putting in time researching and learning about femtosecond laser irradiation, are you planning to apply what you’ve learned to creating something?
Nam: Yes! I am interested in developing sensors to monitor health. I hope to develop sensors to measure glucose from the sweat instead of blood.
NR: Is it possible to detect glucose in sweat?
Nam: Yes, detecting glucose in sweat is possible. But it could only be done using big devices, not wearables. This research is essential to help diabetic patients. Imagine having access to your glucose level anytime and anywhere, in real time. My passion is to fabricate small wearable gadget to achieve that goal.
NR: How would this be possible?
Nam: In wearable devices, smaller parts and components are needed. Wire is needed to conduct electricity, but those on the market are too thick. As such, we need to fabricate everything by ourselves.
I am currently using lasers and special materials to recreate the tiny wires and structures called micrometer patterns. We call the technology “laser direct writing”, whereby the ultrapulse laser can create high energy in a short period of time (also called Femto- or 10-15).
Fabrication could be done in the conventional process, but the step-by-step process is tedious, and it must be done in a vacuum environment. But with laser, we do not need to be in vacuum environment to do that. We could easily draw it on CAD on the PC to create patterns easily at low cost. We also have no limitation on the design! Moreover, with the generation of pure metal, the fabricated 3D pattern could be used as wires. By utilizing this method, I can fabricate metal wires to create smaller devices including wearable glucose detection devices.
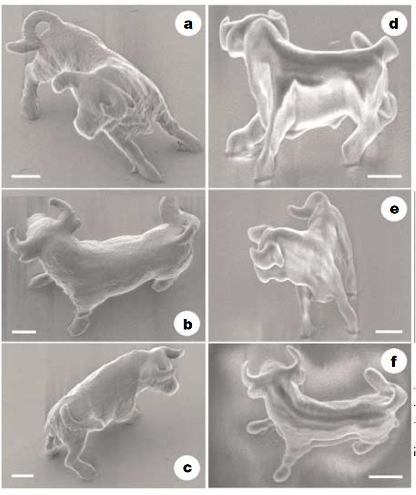
Image of a bull created by the same laser and method Nam uses at the University, utilizing organic material. Scale bar is 2 micron meter. S. Kawata, H.B. Sun, T. Tanaka, K. Takaba, Nature 412 (2001)697.
NR: Since you are in a technology university, what other technology are you currently trying to implement during your research?
Nam: Well, if you consider the use of AI as another technology, then yes, we do use AI to help in simulation. For example, to tweak the laser speed or time, etc. There are many conditions to changing the parameters of a research. AI could help me to narrow down to the top 5 best simulation out of a thousand possibilities. I am currently writing the program now!
NR: Did you experience any challenges during the pandemic?
Nam: That is a good question. Yes, so many things happened since March this year. Our University closed before and after Golden Week, and this is bad news for researchers. I needed to use laser in my research lab because it is not possible to do it remotely. Sometimes, we do not have some equipment in our lab, so we need to go to another university to use the equipment. Due to the pandemic, these places started limiting outsider access. We could not even make a reservation!
Our research was delayed due to broken equipment. At that point in time, anyone traveling in from Tokyo to our university in Nagaoka had to be quarantined for two weeks and the technician could not enter. We decided to fix it remotely by turning on our camera and video calling the company technician. Finally, we managed to fix the equipment by ourselves!
At that point in time, I thought the process was tedious. But upon reflecting, I realized I have learned much more about the equipment. In the past, I would use the equipment without understanding much about it. But after the experience of fixing it, I discovered many interesting points as to why the equipment was built in this manner.
My lab mates and I nearly missed the submission deadline of our papers for the conference and panicked. But luckily, we made it in the end!
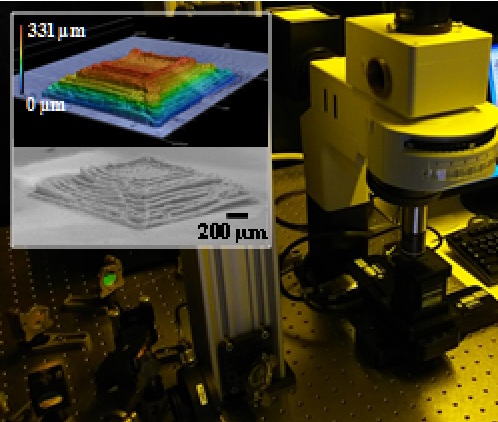
Image of the laser system used by Nam at the University. Image via the Mizoshiri laboratory website.
NR: If you had a chance to innovate and create something to support your lifestyle, what would it be?
Nam: I thought about that question before! If I could, I would love to redesign the washing machine!
The Japanese washing machine is difficult to navigate, even for the locals if they are not used to it. With many buttons and functions, it gets rather confusing. People will have to think about the right setting to select for the right fabric. Moreover, there are some clothing that cannot be handled by the washing machine, it has to be sent to the dry cleaners. I find all these points rather troublesome.
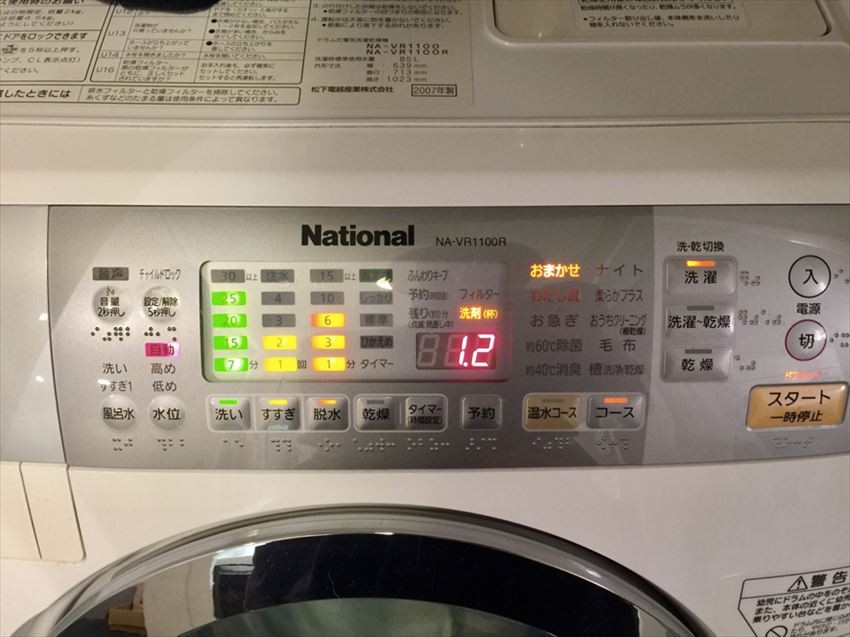
Japanese washing machines equipped with buttons for various washing options. Image via Fun Japan
Besides those challenges, time is needed to operate the washing machine. In general, washing clothes would take about 30 minutes and an additional 30 minutes to dry. Imagine waking up in the morning, realizing you have forgotten to wash it the day before. How might life change if we could do all these in 5 to 10 minutes? What if we could put our clothes into the new washing machine, brush our teeth and have a quick breakfast and have our clothes ready?
I know it might not sound possible now, but I believe this is perfect for people leading a minimalist life! At the same time, a compact washing machine that utilizes less resources would also be great!
NR: What are your hopes and dreams in the future?
Nam: I guess I have many hopes and dreams. But if I had to choose, I would like to work in the research department of a technology company in the future. Hopefully, I would be able to continue my research to develop the technology I am currently working on. I hope to also learn new skills and gain experience from technology companies around the world.
In the future, I also would like to start my own technology company. I aspire to be an all-rounder, having knowledge both in technology as well as business. If I had the chance, I would consider getting an MBA to learn more about the economy and the market. After that, I would like to combine both my knowledge to create products and services that customers need. I have to grow beyond being an Engineer or a Researcher to become someone who understands the needs and applying my skills to create useful solution to the challenges faced.
Student Profile
Name: Ha Phuong Nam (Nam)
Hometown: Hanoi, Vietnam
Research Lab: Micronano Processing Lab
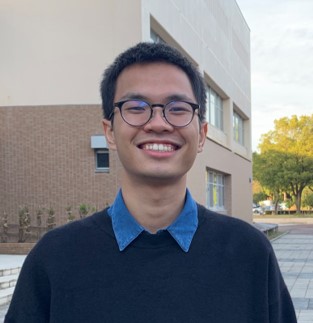